can we do destructive testing for plastic bottles|non destructive testing examples : dealers If nondestructive tests used samples tested for CCI may be used for other tests at same stability time point. Consider CCI testing all samples prior to stability storage, to make sure samples at . Resultado da A Body Energy - Nova Cintra está localizada à 650m do Cemitério Parque da Colina. Uma academia completa, oferece a modalidade de Musculação, com bebedouro, .
{plog:ftitle_list}
web17 de mar. de 2022 · se inscreve no canal : youtube.com/c/GienLiusegue no instagram para mandar ideias de videos: @gienliutiktok: @gienhonliu
For this, the precision required in building testing instruments should be taken care of. For PET bottle testing both destructive and non-destructive tests need to be performed. However, there are some unavoidable destructive test .Destructive (most probabilistic methods): • Internal pressurization results in test sample barrier breach • Submersion or surface wetting is destructive to test samples
By leak testing bottles, manufacturing companies guarantee a high-quality product that is detected for seal, leaks, necks and capacity to holds pressure. These bottle are tested .If nondestructive tests used samples tested for CCI may be used for other tests at same stability time point. Consider CCI testing all samples prior to stability storage, to make sure samples at .The Sepha Multi-Q is a non-destructive CCIT solution that can identify gross holes and micro leaks down to 5 micron in a range of plastic bottles.. Versatile Testing Methods Works in combination with vacuum and pressure decay test .
Leak Detection Test Equipment. For the various testing methods used, manufacturers rely on specific leak detection test equipment. For instance, sometimes multistage linear head equipment gets used with two, three, or four .Do Your Part: Cut Out Plastic Water Bottles. Plastic pollution is an issue that will likely outlive all of us, but that doesn’t mean you can’t start making a difference right now. One of the easiest things you can do — and maybe even .
You might be able to see where the water comes out, but this does not automatically mean that this is the leakage point. Liquids can travel a long way when it comes to leaks. This testing process would be considered a non-destructive test. More common are destructive test methods. What we seek are the ‘yield point’ and/or break.
Non-destructive testing (NDT) is a type of inspection used in plastic manufacturing to test the product's quality without damaging or destroying it. Furthermore, NDT methods are used to detect internal and surface defects in plastic products without causing any damage, making it a valuable testing technique for plastic products that cannot be .So what analysis do we use when the test is destructive? Like many questions that arise where statistics are concerned, the answer is, of course, “it depends.” Crossed Gage R&R for Destructive Testing. Suppose you are conducting a Gage R&R study with 3 operators where each operator measures each part twice. This requires 3x2=6 measurements .
plastic bottle leak test
polarimeter tube name
Non-destructive, reliable and repeatable test method, ideal for testing the integrity of lyophilized and liquid filled vials, ampoules, bottles and other containers. The device shows a pass/fail result in as little as 10 seconds and can identify leaks and channel leaks as low as 5µm (dependent on container type and content). Destructive testing; Non-Destructive testing; Components from batches that are later resold and installed can only be tested in a random and destructive manner. As the need for testing increases, the cost of the scrap caused by the test rises. As a result, a complete test is methodologically impossible. On this note, the field of non .
The future of destructive testing lies in its integration with other testing methods, such as non-destructive testing and computer simulations. By combining these methods, engineers can obtain a more comprehensive understanding of material properties and behavior, leading to improved product designs and manufacturing processes.destructive testing (NDT) for inspection and non-destructive evaluation (NDE) for the volumetric examination of plastic pipes. It is only within the last 2 – 5 years, organizations such as ASTM E07 or F17 and ISO TC138 have worked to introduce standardized inspection methods for polyethylene (PE ) heat-fusion and electro-fusion (EF) joints.ISBT Plastic Bottle Test Method 2004; Typical Top-Load Testing System. 50-mm vented compression plate; MultiTest 5-xt (Superseded by OmniTest 5 universal testing machine . We do not provide medical advice, if you search for medical information you must always consult a medical professional before acting on any information provided. Your .
The liquid penetrant test is one of the most widely used Non-Destructive Test (NDT) methods. It can be used to inspect almost all non-porous materials such as metals, plastics, ceramics, etc. We can only detect any surface discontinuity (or irregularity) such as surface cracks, porosity, pinholes, etc. by this test method.What is the difference between destructive and non-destructive testing? Destructive tests show how and when a material will fail whilst non-destructive tests highlight pre-existing flaws in the material, such as cracks or corrosions, that indicate it could fail in the future.. As destructive testing can only be conducted by damaging the test specimen, it can be costly for the .
polarimeter tube temperature
It can be used for speedy determination of the amount of CO2 loss through the bottle wall, the closure, and across the seal. Plastic beverage bottles do a near-perfect job of holding their liquid contents. The real challenge is holding CO2 gas, which can travel through the bottle wall, the cap, or the seal where cap and bottle meet.One type of leak test for vials is the pressure decay test, a non-destructive leak testing method. Facebook; . The pressure decay leak test is often used to detect leaks and micron holes in plastic or glass vials that contain a variety of .Ultrasonic Testing (UT) is a widely used non-destructive testing method that utilizes high-frequency sound waves to detect flaws, defects, and irregularities . including manufacturing, construction, aerospace, and more. In this article, we .Ultrasonic non destructive testing is a method of characterizing the thickness or internal structure of a test piece through the use of high frequency sound waves . Other important applications include measuring the thickness of molded .
Vacuum Decay Method technology allows testing that identifies the presence of leaks in hermetically sealed containers in a non-destructive and non-invasive manner. It can be used to test plastic, glass or metal containers - making it effective both for pharmaceutical and food & beverage industries - and rigid or flexible packaging. As a result, to keep up with production and guarantee accuracy in testing, additional stations may be required to test larger containers. Do not settle for a leak test that barely meets your quality requirements. Among other things, hot production bottles and line delays can contribute to variations in test results making defects harder to .
The global campaign to gain control of plastic waste is one of the fastest-growing environmental causes ever mounted. Yet it hasn’t been enough to make a dent in the growing tonnage of discarded . Both destructive and non-destructive testing can give very reliable results. Destructive testing can only test a small number of samples (lot sampling). Non-destructive testing, on the other hand, can test entire batches. NDT is also a better alternative to find discontinuities and defects in a part. Non-Destructive Testing Methods Visual testing What is destructive testing? Destructive testing evaluates materials and components by subjecting them to extreme conditions that lead to “plastic deformation,” i.e., failure, damage, or even destruction. Common destructive testing methods include tension, compression, impact, and hardness tests. Here are the most common DT procedures:
Testing the integrity of package seals helps ensure that food packaging provides required product protection. Sustainable packaging alternatives, lower cost packaging, and variations in production line sealing parameters are frequently assessed with seal integrity tests. With the renewed interest in sustainable packaging, alternate structures .Test no. Action; 1. Look at the sample. Is it transparent, translucent or opaque? 2. Feel the sample. Does it bend? Can it be scratched? What does the surface feel like? 3. Cut the sample with a sharp knife. Does it cut easily? Are the edges smooth or jagged? Does it crumble or flake? 4. Subject the sample to a float test. Does it float or sink?We were founded in 1974 and to date, have delivered more than 3,000 machines responsible for testing over 50 billion containers annually. Our leak testing equipment ranges from manual testing equipment for lab and sampling applications to high-speed rotary leak testing systems. Contact us to learn how we can solve your product leak testing .Non-Destructive Micro Crack Detection in Modern Materials Joerg SCHORS, K.-Wolfram HARBICH, Manfred P. HENTSCHEL, Axel LANGE, Federal Institute for Materials Research and Testing (BAM), Germany Abstract. For the purpose of nondestructive crack detection X-ray refraction is ap-plied. Micro cracks are essential indicators for fatigue and degradation.
Microplastics, small plastic pieces <5 mm intentionally produced to be used in consumer products (e.g. as exfoliants in cosmetics) and in activities as abrasives (e.g. air blasting) (primary microplastics) or resulting from the fragmentation of larger objects (secondary microplastics), are highly persistent contaminants potentially harmful to organisms or .
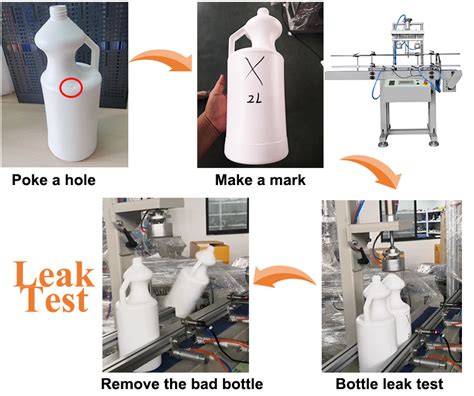
plastic bottle leak detection
polarimeter tubes
WEB12/11/2023 02h03 Atualizado há 3 meses. Grêmio e Corinthians se enfrentam neste domingo, às 16h (de Brasília), na Arena, em Porto Alegre, pela 34ª rodada do .
can we do destructive testing for plastic bottles|non destructive testing examples